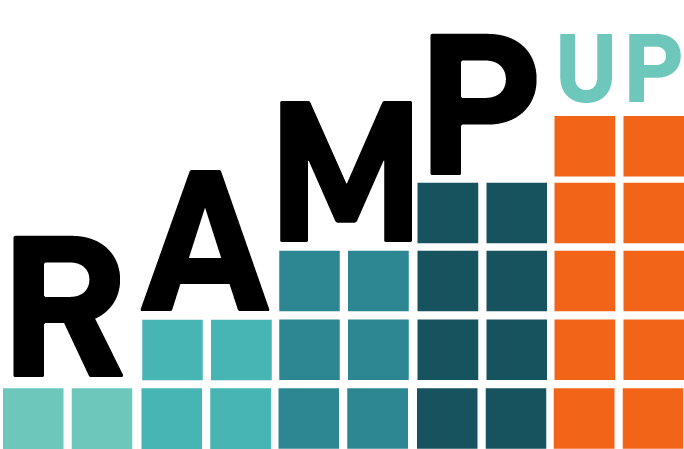
When we are facing ramp-up situation with manufacturing and supply chain organizations, we usually faced many disruptive events which unable us and the operation organization to provide the required finish goods according the sales plan.
In this article, I will review several methods to deal with ramp-up situations within manufacturing and supply chain organizations:
First of all – how can we recognize we are in Ramp-up situation?
One of the biggest mistakes of manufacturing organizations is the missconception about its actual situation, in some cases the management feels its only regular increase with demand and therefore don’t take the requried measurement to contain it and face failure soon or in other hand, misjudgment and declare ramp up phase, which results with rapid actions regarding inventory increase, infrastructure build up and labor recuruitment.
So how we recognize Ramp up?
It is common to consider that any increase of product demand over 25% on a sepcific period of time compare to the previous period which results with required increase of ~ 25% or more with constrained resource like: material sourcing, head count, production facility.
The KPI differ from industry to industry, in capital equipment manufacture 25% is widely agreed, in other industires, the KPI could be much higer or much lower.
Other way to recognuze the situation is the timeframe required to fulfill the increased demand, which means if we need more than 6 months to build up the required capacity to withstand the new demand, then we are in ramp-up situation.
Second action – how to define the operative drivers to contain the ramp up?
In order to answer the increasing demand for products/finish goods, the important action required is to identify the main constrains and operative drivers to contain the ramp up. For example:
Material readiness and lead time to source the goods. suppliers capacity to deliver the required level of units in specific time frame, for example: X units per week/month.
Production facility area/foot print, number of assembly slots, processing machines, clean room, machinery, equpment, tools etc. for example, each production slots can produce Y units in std working shift of 8 hours.
Proffesional human resource required to manufacture the products/finish goods.
Thirs rule – to whom we deal first?
The basic rule which of the constrains to deal first is according the identification of the phrase known from Theory of constrains, or simple Project managing is the “Critical path”, or the resource which set the tempo of the entire supply chain.
Another way to identify the “Critical pth” or the “bottle neck” is to increase the specific resource which in results increase the over whole system thoughput.
If increase of the resource wouldn’t results in higher thtoughput, then this resource is not consider to be “bottle neck” and we should look for it in other place.
In general, once we do find the “bottle neck” and resolve its shortage, we will soon face another or new “bottle neck” as well as we increase the demand from the system.
Ways to resolve “bottle necks”:
Increase thoughput by adding labor resource, manufacture machines of tools, increase purchasing volumes in order to increase inventory and utilize more production capability (working overtime/double working shifts).
Last rule – what do we need to be careful about when ramp up?
Once we are on the run, we usually forget that after the pick we will have the slow down, once of the important rule of ramp up is to prepare for the slow which will come right after.
Smart supply chain managers, build a ramp up mechanism such can shrink back to normal production with minimum impact of the operations KPI. ways to do so are:
Using same facility to contain higher demand without investing with additional infrastructure.
Define flexible supply resource which can increase on demand and decrease when ramp up is stabilized with minimum risk for dead stock.
Utilizing head count and human resource and optimize the labor resource in order to minimize letoffs after ramp up period.
Aftermath:
Managing ramp up is not easy task for supply chain managers, it requires fast and clear understanding of the situation as well as the drivers to solve it.